GP PWC
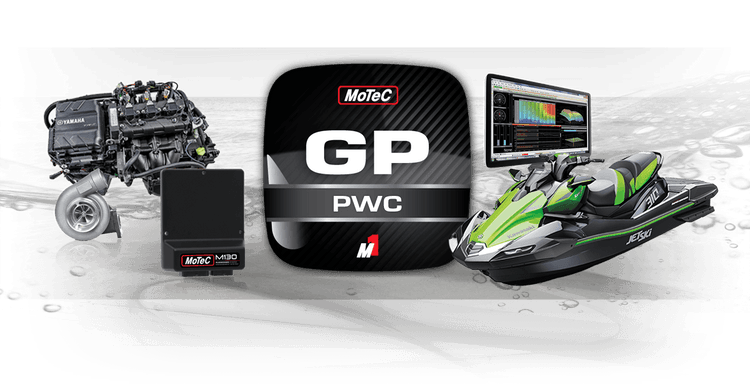
MoTeC’s M1 GP PWC package contains specific features unique to PWC applications, and is a versatile and adaptable platform for the operation of port injection engines in personal watercraft. The GP WCC is based on the GP Marine Package.
This single product can be configured in a wide range of complexities, from single engine control to multi-throttle, quad cam boosted with two injectors per cylinder and many other features. Configurable engine timing modes accommodate most modern engine drive systems.
Various auxiliary features are included, such as thrust limiting, knock control and launch control. It also supports many systems found on marine vessels that may be useful in a racing context.
Features
- Operates 1 to 8 cylinder (M130/M170) or 1 to 12 cylinder (M150/M190) port injection engines.
- 2-port injector control (peak and hold or saturated) per cylinder ('high/low' setting) with adjustable balancing table.
- The fuel volume calculation takes into account the delay effects resulting from the secondary (high) injector position.
- Configurable engine timing modes.
- Configurable top dead center for each cylinder allows for odd-firing engines.
- Configurable ignition output pin for each cylinder allows for coil-on-plug or wasted spark and distributor systems.
- Configurable camshaft control from 1 to 4 cams, plus 1 switched camshaft.
- Dual bank lambda control is supported; requires optional LTC with Bosch LSU 4.9 sensor or LTC NTK with NTK sensor.
- Configurable integrated knock for each cylinder with up to 4 assignable knock sensors (hardware dependent) and selectable center frequencies.
- Sensor calibrations available for many common automotive sensors.
- Physical settings for engine displacement, fuel density and molar mass, stoichiometric ratio, and injector characteristics allow for simplified engine start-up prior to tuning.
- Quick and easy engine tuning using the engine efficiency map.
- Modeling engine load based on intake manifold pressure and temperature. Alternatively, allows engine load based on throttle.
- Calculating the engine load temperature allows correction of the inlet air temperature.
- Engine speed limitation with ignition cut and/or fuel cut with individual decay rates for smooth power reduction via engine speed limit decay table.
- Fuel transient compensation using fuel film modeling.
- Nitrous system with two stages of actuation and additional fuel pumps, bottle heater control and pressure sensor.
- Test settings for most outputs including injection and ignition outputs for easy setup.
- Assisted engine starting with dedicated fuel volume and idle compensation during crank start and post-start.
- Configurable turbocharger boost control (using a normal or inverted solenoid output).
- Coolant temperature compensations for engine speed limit, ignition timing, fuel mixture and boost limit.
- Cooling pump output with PWM control.
- Coolant pump after-run functionality, optionally with additional pump output.
- Engine oil pressure and temperature.
- Support for up to 3 switched fuel pump outputs. Demand-based activation of fuel flow and nitrous injection.
- Fuel Flow Supply and Fuel Return Flow Sensor.
- Fuel tank level.
- Gear position detection.
- Race timing system with compensation tables for ignition timing compensation, fuel mixture aiming, boost limit and acceleration limit.
- Closed loop idle control system using ignition, pull-by-wire drive or idle solenoid.
- Idle bypass control with stepper motor supported.
- Engine Load Average Channel with tables for Engine Speed Limit, Ignition Timing Trim, Fuel Mixture Target, Boost and Throttle Limit.
- Intake manifold flap support.
- Intake manifold runner support.
- Closed loop alternator control.
- Total engine running time for engine hour logging.
- Dual bank drive by wire throttle servo control.
- Throttle lever sensor with translation table.
- Use of a throttle lever sensor or throttle position sensor in the case of a cable throttle.
- Pulsed tachometer output with configurable output pin and scale.
- Vehicle speed limit control system (based on DBW accelerator).
- Configurable warning system with light output and CAN.
- Auxiliary timing system with tables for ignition timing compensation, fuel volume compensation and fuel mixture targeting.
- The ECU CAN receive from a defined CAN ID for receiving data from MoTeC devices. Support of 1 (M130/M170) or 3 (M150/M190) CAN buses.
- ECU CAN Transmits from most common channels using standard MoTeC CAN models.
- Custom CAN transmission (4 messages).
- GPS acquisition and recording via CAN and RS232.
- Driver switches.
- 8 configurable driver switches, 8 rotary switches and support for MoTeC keyboard and rotary controller, each with 10 positions that can be simultaneously mapped to launch control, anti-lag, race time reset, maximum engine speed limit, throttle lever translation, ignition timing, fuel mixture aiming, boost limit, cruise set, cruise up, cruise down.
- MoTeC device support: E8XX, PDM, SLM, Keyboard, Rotary Controller.
- Configurable security for multiple users with different access options.
- Lap distance, lap time and lap number via BR2 or switched input, with split and sector options.
- Launch control.
- Configurable cruise and slow modes.
- Configurable pull cord switch support.
- Configurable Anti-Lag with Ignition Timing Limit Advance, Fuel Volume Compensation, Ignition Cut, Fuel Cut, Engine RPM Limit, Boost Target and Throttle Target tables.
- 5 auxiliary outputs for PWM control of actuators added:
- Duty cycle using engine speed and throttle or manifold pressure shaft.
- Activation based on intake manifold pressure or throttle position.
- Auxiliary Output 1 includes tables for ignition timing compensation, fuel volume compensation, and fuel mixture target.
- Optional integrations:
- Optional channels for additional sensors via input pin and/or CAN message, including:
- Airbox mass flow, pressure and temperature.
- Ambient temperature and pressure.
- Impulse pressure.
- Coolant pressure and temperature.
- Engine crankcase pressure.
- Engine oil level.
- Engine oil pressure.
- Exhaust pressure bank 1 and bank 2.
- Exhaust temperature via TCA thermocouple amplifier, generic CAN or E888 for manifold, manifold Bank 1 and Bank 2 and up to 12 cylinders (hardware dependent).
- Lambda Exhaust via LTC, LTC NTK or PLM for Manifold and up to 12 cylinders (hardware dependent).
- Fuel Composition, Flow, Temperature and Pressure.
- Fuel flow supply and return.
- Fuel tank level.
- Fuel water content.
- Gear position.
- Input mass flow.
- Intercooler temperature and spray control.
- Jet nozzle pressure and angle, intake pressure and temperature.
- Steering angle and pressure.
- Turbocharger speed, temperature and pressure.
- Turbocharger bypass valve.
- Vehicle acceleration – longitudinal, lateral and vertical.
- Optional channels for additional sensors via input pin and/or CAN message, including:
Pinout Example
M130M A connector — 34 ways
Mating connector: Tyco Superseal 34 Position Keying 1 – MoTeC #65044
Pin number | Designation | Full name | Description |
---|---|---|---|
A01 | OUT_HB2 | Half bridge exit 2 | |
A02 | SEN_5V0_A | 5.0VA Sensor | Sensor supply voltage 5V |
Answer A03 | IGN_LS1 | Low side ignition 1 | Ignition cylinder 1 |
A04 | IGN_LS2 | Low Side Ignition 2 | Ignition cylinder 2 |
A05 | IGN_LS3 | Low side ignition 3 | Ignition cylinder 3 |
A06 | IGN_LS4 | Low side ignition 4 | Ignition cylinder 4 |
A07 | IGN_LS5 | Low side ignition 5 | |
A08 | IGN_LS6 | Low side ignition 6 | |
A09 | SEN_5V0_B | 5.0VB Sensor | 5V sensor power supply |
Answer 10 | BAT_NEG1 | Negative Battery | |
Answer 11 | BAT_NEG2 | Negative Battery | |
Answer 12 | IGN_LS7 | Low Side Ignition 7 | |
Answer 13 | IGN_LS8 | Low side ignition 8 | |
Answer 14 | AV1 | Analog voltage input 1 | Intake manifold pressure sensor |
Answer 15 | AV2 | Analog voltage input 2 | |
Answer 16 | AV3 | Analog voltage input 3 | Fuel pressure sensor |
Answer 17 | AV4 | Analog voltage input 4 | Engine oil pressure sensor |
Answer 18 | OUT_HB1 | Half bridge exit 1 | |
A19 | INJ_PH1 | Peak retention injector 1 | Fuel Injector Cylinder 1 |
Answer 20 | INJ_PH2 | Peak retention injector 2 | Fuel injector cylinder 2 |
A21 | INJ_PH3 | Peak retention injector 3 | Fuel Injector Cylinder 3 |
ANSWER 22 | INJ_PH4 | Peak retention injector 4 | Fuel Injector Cylinder 4 |
A23 | INJ_LS1 | Low Side Injector 1 | Impulse solenoid |
A24 | INJ_LS2 | Low Side Injector 2 | |
A25 | AV5 | Analog voltage input 5 | Exhaust Pressure Bank 1 Sensor |
A26 | BAT_POS | Positive Battery | ECU battery voltage |
A27 | INJ_PH5 | Peak retention injector 5 | |
A28 | INJ_PH6 | Peak retention injector 6 | |
A29 | INJ_PH7 | Peak retention injector 7 | |
Answer 30 | INJ_PH8 | Peak retention injector 8 | |
A31 | OUT_HB3 | Half bridge exit 3 | Throttle servo bank 1 motor output |
A32 | OUT_HB4 | Half bridge exit 4 | Throttle servo bank 1 motor output |
A33 | OUT_HB5 | Half bridge exit 5 | |
Answer 34 | OUT_HB6 | Half bridge exit 6 |
M130M Connector B — 26-way
Mating connector: Tyco Superseal 26 Position Keying 1 – MoTeC # 65045
Pin number | Designation | Full name | Description |
---|---|---|---|
B01 | UDIG1 | Universal digital input 1 | Engine speed sensor |
B02 | UDIG2 | Universal digital input 2 | Camshaft speed sensor |
B03 | AT1 | Analog temperature input 1 | Intake air temperature sensor |
B04 | AT2 | Analog temperature input 2 | Coolant temperature sensor |
B05 | AT3 | Analog Temperature Input 3 | Engine oil temperature sensor |
B06 | AT4 | Analog temperature input 4 | |
B07 | BEAT 1 | Detonation input 1 | Beat 1 |
B08 | UDIG3 | Universal Digital Input 3 | Throttle servo bank 1 position sensor |
B09 | UDIG4 | Universal digital input 4 | |
B10 | UDIG5 | Universal Digital Input 5 | |
B11 | UDIG6 | Universal Digital Input 6 | |
B12 | BAT_BAK | Battery Backup | |
B13 | BEAT 2 | Detonation input 2 | |
B14 | UDIG7 | Universal digital input 7 | |
B15 | SEN_0V_A | Sensor 0V A | Sensor supply voltage 0V |
B16 | SEN_0V_B | Sensor 0V B | Sensor supply voltage 0V |
B17 | CAN_HI | CAN Bus 1 High | |
B18 | CAN_LO | CAN Bus 1 Low | |
B19 | SEN_6V3 | 6.3V Sensor | Sensor supply voltage 6.3 V |
B20 | AV6 | Analog voltage input 6 | Driver Rotary Switch 1 |
B21 | AV7 | Analog voltage input 7 | Throttle lever sensor tracking |
B22 | AV8 | Analog voltage input 8 | Main throttle lever sensor |
B23 | ETH_TX+ | Ethernet+ transmission | Green/White Ethernet |
B24 | ETH_TX- | Ethernet Transmission- | Green Ethernet |
B25 | ETH_RX+ | Ethernet+ reception | Orange/White Ethernet |
B26 | ETH_RX- | Ethernet Reception- | Orange Ethernet |
M150M Connector A – 34 Ways
Mating connector: Tyco Superseal 34 Position Keying 2 – MoTeC # 65067Pin number | Designation | Full name | Description |
---|---|---|---|
A01 | AT5 | Analog Temperature Input 5 | Engine oil level sensor |
A02 | AT6 | Analog temperature input 6 | Water temperature sensor |
Answer A03 | AV15 | Analog voltage input 15 | |
A04 | AV16 | Analog voltage input 16 | |
A05 | AV17 | Analog voltage input 17 | Throttle lever sensor tracking |
A06 | IGN_LS9 | Low side ignition 9 | |
A07 | IGN_LS10 | Low side ignition 10 | |
A08 | IGN_LS11 | Low side ignition 11 | |
A09 | IGN_LS12 | Low side ignition 12 | |
Answer 10 | SEN_5V0_C1 | 5.0VC Sensor | 5V sensor power supply |
Answer 11 | LA_NB1 | Lambda narrow input 1 | |
Answer 12 | LA_NB2 | Lambda 2 Narrow Entry | |
Answer 13 | BEAT 3 | Detonation input 3 | |
Answer 14 | BEAT 4 | Detonation input 4 | |
Answer 15 | DIG2 | Digital input 2 | |
Answer 16 | DIG3 | Digital input 3 | |
Answer 17 | DIG4 | Digital input 4 | |
Answer 18 | SEN_5V0_C2 | 5.0VC Sensor | 5V sensor power supply – |
A19 | SEN_5V0_B2 | 5.0VB Sensor | 5V sensor power supply |
Answer 20 | LIN | LIN Bus | |
A21 | RS232_RX | RS232 Receive | GPS |
ANSWER 22 | RS232_TX | RS232 transmission | |
A23 | DIG1 | Digital input 1 | |
A24 | BAT_NEG3 | Negative Battery | Floor |
A25 | BAT_NEG4 | Negative Battery | Floor |
A26 | SEN_0V_C1 | Sensor 0V C | Sensor power supply 0V |
A27 | SEN_0V_C2 | Sensor 0V C | Sensor power supply 0V |
A28 | CAN3_HI | CAN Bus 3 High | |
A29 | CAN3_LO | CAN Bus 3 Low | |
Answer 30 | CAN2_HI | CAN Bus 2 High | |
A31 | CAN2_LO | CAN Bus 2 Low | |
A32 | BAT_NEG5 | Negative Battery | |
A33 | SEN_0V_B1 | Sensor 0V B | Sensor power supply 0V |
Answer 34 | SEN_0V_A1 | Sensor 0V A | Sensor power supply 0V |
M150M Connector B – 26-way
Mating connector: Tyco Superseal 26 Position Keying 3 – MoTeC # 65068Pin number | Designation | Full name | Description |
---|---|---|---|
B01 | OUT_HB9 | Half bridge exit 9 | |
B02 | OUT_HB10 | Half bridge exit 10 | |
B03 | UDIG8 | Universal digital input 8 | Fuel water content switch |
B04 | UDIG9 | Universal Digital Input 9 | Engine start switch |
B05 | UDIG10 | Universal Digital Input 10 | |
B06 | UDIG11 | Universal Digital Input 11 | |
B07 | UDIG12 | Universal digital input 12 | |
B08 | INJ_LS5 | Low Side Injector 5 | |
B09 | INJ_LS3 | Low Side Injector 3 | |
B10 | AV9 | Analog voltage input 9 | Main throttle lever sensor |
B11 | AV10 | Analog voltage input 10 | Throttle servo position sensor tracking |
B12 | AV11 | Analog voltage input 11 | |
B13 | BAT_POS | Positive Battery | ECU Power Relay |
B14 | INJ_LS6 | Low Side Injector 6 | |
B15 | INJ_LS4 | Low Side Injector 4 | |
B16 | AV12 | Analog voltage input 12 | Coolant pressure sensor |
B17 | AV13 | Analog voltage input 13 | Fuel tank level sensor |
B18 | AV14 | Analog voltage input 14 | |
B19 | BAT_POS | Positive Battery | |
B20 | OUT_HB7 | Half bridge exit 7 | |
B21 | OUT_HB8 | Half bridge exit 8 | |
B22 | INJ_PH9 | Peak retention injector 9 | |
B23 | INJ_PH10 | Peak retention injector 10 | |
B24 | INJ_PH11 | Peak retention injector 11 | |
B25 | INJ_PH12 | Peak retention injector 12 | |
B26 | SEN_5V0_A | 5.0VA Sensor | 5V Power Sensor |
M150M Connector C – 34 ways
Mating connector: Tyco Superseal 34 Position Keying 1 – MoTeC #65044Pin number | Designation | Full name | Description |
---|---|---|---|
C01 | OUT_HB2 | Half bridge exit 2 | Positive throttle servo motor |
C02 | SEN_5V0_A | 5.0VA Sensor | 5V sensor power supply |
C03 | IGN_LS1 | Low side ignition 1 | Ignition cylinder 1 |
C04 | IGN_LS2 | Low Side Ignition 2 | Ignition cylinder 2 |
C05 | IGN_LS3 | Low side ignition 3 | Ignition cylinder 3 |
C06 | IGN_LS4 | Low side ignition 4 | Ignition cylinder 4 |
C07 | IGN_LS5 | Low side ignition 5 | Fuel pump relay |
C08 | IGN_LS6 | Low side ignition 6 | |
C09 | SEN_5V0_B | 5.0VB Sensor | 5V sensor power supply |
C10 | BAT_NEG1 | Negative Battery | |
C11 | BAT_NEG2 | Negative Battery | |
C12 | IGN_LS7 | Low Side Ignition 7 | Engine starter motor relay |
C13 | IGN_LS8 | Low side ignition 8 | |
C14 | AV1 | Analog voltage input 1 | Main throttle servo position sensor |
C15 | AV2 | Analog voltage input 2 | |
C16 | AV3 | Analog voltage input 3 | Engine oil pressure sensor |
C17 | AV4 | Analog voltage input 4 | Intake manifold pressure sensor |
C18 | OUT_HB1 | Half bridge exit 1 | Negative throttle servo motor |
C19 | INJ_PH1 | Peak retention injector 1 | Injector Cylinder 1 |
C20 | INJ_PH2 | Peak retention injector 2 | Injector Cylinder 2 |
C21 | INJ_PH3 | Peak retention injector 3 | Injector Cylinder 3 |
C22 | INJ_PH4 | Peak retention injector 4 | Injector Cylinder 4 |
C23 | INJ_LS1 | Low Side Injector 1 | |
C24 | INJ_LS2 | Low Side Injector 2 | |
C25 | AV5 | Analog voltage input 5 | |
C26 | BAT_POS | Positive Battery | |
C27 | INJ_PH5 | Peak retention injector 5 | |
C28 | INJ_PH6 | Peak retention injector 6 | |
C29 | INJ_PH7 | Peak retention injector 7 | |
C30 | INJ_PH8 | Peak retention injector 8 | |
C31 | OUT_HB3 | Half bridge exit 3 | |
C32 | OUT_HB4 | Half bridge exit 4 | |
C33 | OUT_HB5 | Half bridge exit 5 | |
C34 | OUT_HB6 | Half bridge exit 6 |
M150M Connector D — 26 Ways
Mating connector: Tyco Superseal 26 Position Keying 1 – MoTeC # 65045Pin number | Designation | Full name | Description |
---|---|---|---|
D01 | UDIG1 | Universal digital input 1 | Engine speed reference |
D02 | UDIG2 | Universal digital input 2 | Engine synchronization |
D03 | AT1 | Analog temperature input 1 | Coolant temperature sensor |
D04 | AT2 | Analog temperature input 2 | Intake air temperature sensor |
D05 | AT3 | Analog Temperature Input 3 | Engine oil temperature sensor |
D06 | AT4 | Analog temperature input 4 | Exhaust gas temperature sensor |
D07 | BEAT 1 | Detonation input 1 | Beat 1 |
D08 | UDIG3 | Universal Digital Input 3 | |
D09 | UDIG4 | Universal digital input 4 | Pull cord switch |
D10 | UDIG5 | Universal Digital Input 5 | Vehicle Drive Trim Up/Down Switch |
D11 | UDIG6 | Universal Digital Input 6 | Vehicle Drive Trim Up/Down Switch |
D12 | BAT_BAK | Battery Backup | |
D13 | BEAT 2 | Detonation input 2 | Beat 1 |
D14 | UDIG7 | Universal digital input 7 | |
D15 | SEN_0V_A | Sensor 0V A | Sensor power supply 0V |
D16 | SEN_0V_B | Sensor 0V B | Sensor power supply 0V |
D17 | CAN1_HI | CAN Bus 1 High | |
D18 | CAN1_LO | CAN Bus 1 Low | |
D19 | SEN_6V3 | 6.3V Sensor | Power Supply Sensor 6.3V |
D20 | AV6 | Analog voltage input 6 | |
D21 | AV7 | Analog voltage input 7 | |
D22 | AV8 | Analog voltage input 8 | Fuel pressure sensor |
D23 | ETH_TX+ | Ethernet+ transmission | Green/White Ethernet |
D24 | ETH_TX- | Ethernet Transmission- | Green Ethernet |
D25 | ETH_RX+ | Ethernet+ reception | Orange/White Ethernet |
D26 | ETH_RX- | Ethernet Reception- | Orange Ethernet |