GPRP Drag
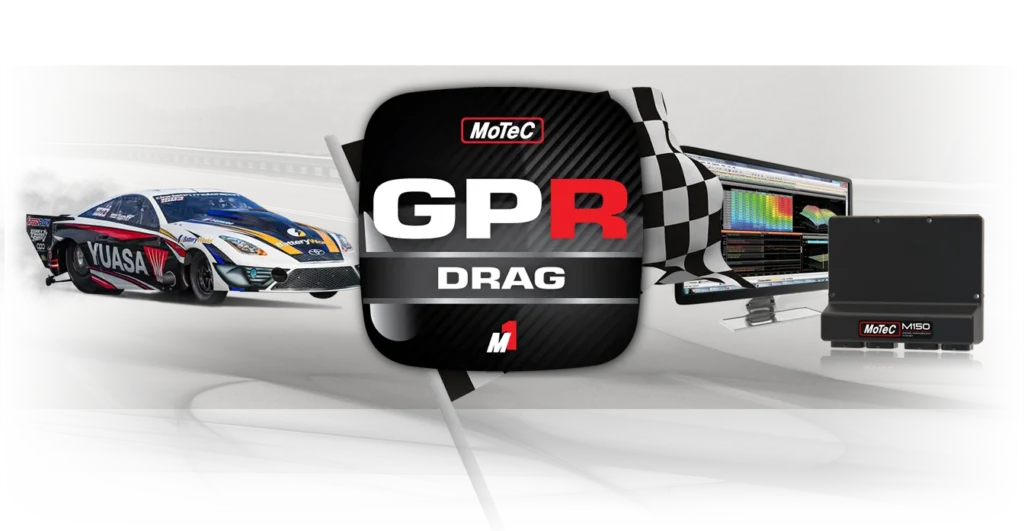
MoTeC's M1 GPR Drag Package is a versatile tuning platform that was developed specifically for drag racing applications.
It is a highly adaptable solution that can be configured to handle a multitude of complexities, from the simplest of engines to a multi-throttle, quad-cam engine, enhanced with two injectors per cylinder, a sequential gearbox, nitrous system and many other high-performance enhancements.
Features
Tailor made for Drag
MoTeC’s GPR Trawl Package builds on the GPR Package, with additional features and improvements specifically for trawl applications, including:
- Additional vehicle speed and run time conditions at auxiliary outputs
- Auxiliary outlet fuel and ignition trims
- Boost Servo System – Use a servo motor to control a wastegate or use an additional throttle servo to bleed boost air from the compressor. This can help with compressor surge, act as a wastegate, or control boost with greater response.
- Clutch position limit for launch condition – can be upgraded with a switch, for drag vehicles with clutch and critical 'bite' position.
- Improved tuning resolution for highly tuned engines
- Improved sensor and calculation resolution critical for drag racing
- Individual cylinder fuel trim for respective exhaust temperature
- Warnings with engine speed and throttle limits for primary and secondary injector duty cycle
- Support automatic transmission gear detection and converter slip monitoring
- Gear output shaft speed, fuel and ignition trims, plus acceleration and thrust limits.
- Closed loop Control of engine torque by altering ignition timing. Used for traction control and launch control. By varying ignition timing rather than cutting ignition events, turbo lag in large turbos is reduced.
- Improved launch control for more vehicle configurations – faster boost build, multi-step staging, nitrous integration, and traction control integration.
- Improved Nitro Control – bottle pressure warning and additional conditions for use during launch control and time after launch.
- Improved Race Time triggering strategy – more configurable, false start detection and reset, and integration with traction control for acceleration limitation.
- Enhanced traction control using ignition timing control. Limitation based on wheel speed or engine speed for use with automatic transmissions.
- Shift light output
- Additional sensor inputs:
- Sleep position x 4, recording at 1000Hz (with optional level 3 recording)
- Transmission temperature x 2
- Transmission pressure x 2
- Tire pressure x 4
- Tire temperature x 4
- Wheelie bar pressure x 2
- Transmission brake control with enhanced 'bump' functionality (pulse or PWM modes) for perfect vehicle preparation.
- Fuel and ignition based on vehicle speed and throttle limit.
- Calculation of vehicle speed estimation using wheel speeds, GPS speed and time-based speed after launch. Different estimation modes for various vehicle configurations.
- Dump valve pressure control by dual CO2 style solenoids and pressure feedback
- Live adjustment for tire growth with speed
Common to GPR package variants
- Fits 1 to 12 cylinder injected engines
- Configurable engine timing modes for many common engine types. See Engine Timing Modes section for current details..
- Configurable top dead center for each cylinder allows for odd-firing engines.
- Configurable ignition output pin for each cylinder allows for coil-on-plug or wasted spark and distributor ignition systems.
- Configurable integrated knock for each cylinder with up to 4 assignable knock sensors (hardware dependent) and selectable center frequencies.
- Configurable camshaft control from 1 to 4 cams, plus 1 switched camshaft.
- Dual bank lambda control supported; requires optional LTCD with Bosch LSU4.9 sensor or LTCD NTK with NTK sensor.
- Physical settings for engine displacement, fuel density + molar mass, stoichiometric ratio and injector characteristics allow for simplified engine start-up prior to tuning.
- Quick and easy engine tuning using the engine efficiency map.
- Modeling of engine load based on intake manifold pressure and intake manifold temperature. Alternatively, for example when using individual throttle bodies, the throttle position can be used.
- 2-port injector control (peak and hold or saturated) per cylinder ('high/low' setting) with adjustable balancing table.
- The fuel volume calculation takes into account the delay effects resulting from the secondary injector installation position (high).
- Calibrations available for many common automotive sensors.
- Fuel transient compensation using fuel film physics modeling.
- Nitrous system with two stages of actuation and additional fuel pumps, bottle heater control and pressure sensor.
- Support for MoTeC devices: ADR, E8XX, PDM, SLM, Video Capture Systems, Displays and Loggers.
- Test settings for most outputs – including injection and ignition outputs – to make setup easier.
- Turbocharger boost/wastegate control by solenoids or servo motor.
- Configurable anti-lag for single turbo with ignition timing limit, fuel volume compensation, ignition cut, engine speed limit, boost aiming and throttle aiming tables.
- Support of a turbocharger bypass valve control
- Support dual cooling fan outputs (PWM controlled)
- Air conditioning support with switched outlet control
- Coolant temperature compensations for engine speed limit, ignition timing, fuel mixture, boost limit.
- Coolant pump output with PWM control
- Coolant pump after-run functionality, optionally with additional pump output.
- Engine speed limitation with ignition cut-off and/or fuel cut-off
- Multiple switched fuel pump outputs with nitrous trigger
- Closed loop fuel pressure control by PWM driving the fuel pump
- Fuel Flow Supply Sensor and Fuel Return Flow Sensor
- Gearbox position detection via optional dual sensor or engine speed/wheel speed estimation
- Gear shift request via upshift switch/downshift switch or shift lever force sensor
- Gearbox shift support with ignition cut, fuel cut, throttle blip and corresponding engine speed in forward gears.
- Intercooler temperature and spray control based on differential temperature with dedicated temperature sensor and switched pump output.
- Differential oil temperature control with dedicated temperature sensor and switched pump output
- Calculation of engine load temperature, allows correction of inlet air temperature (compensation for heat absorption effect, etc.).
- Distance, time and lap number via BR2, GPS or switched input, with split and sector options.
- Configurable launch control with tables for engine speed, throttle limit, thrust aiming and fuel volume compensation.
- Race timing system with compensation tables for ignition timing compensation, fuel mixture aiming, boost limit and throttle limit.
- Closed loop idle control system using ignition, pull-by-wire drive or idle solenoid.
- Idle bypass control with stepper motor supported
- Average Engine Load Channel with tables for engine speed limit, ignition timing compensation, fuel mixture targeting, turbo limit and throttle limit.
- Intake manifold flap support (2-bank position feedback actuator)
- Intake manifold support (actuator with position feedback)
- Assisted engine starting with dedicated fuel volume and idle compensation during crank start and post-start.
- Closed loop alternator control
- Total engine running time for engine hour recording
- Configurable security for multiple users
- Setting the brake state using a switch or pressure sensor
- Brake vacuum control system with dedicated switched pump
- Setting the clutch state using a switch, a position sensor or a pressure sensor.
- Clutch slip calculation
- ECU internal G-force (acceleration) – longitudinal, lateral, vertical
- The ECU CAN receive from a defined CAN ID for receiving data from MoTeC devices. Support of one CAN bus (M130/M170) or three CAN buses (M150/M190) (some M1 models may not be supported currently in this package).
- ECU CAN transmits the most common channels using standard MoTeC CAN models.
- 8 configurable toggle switches and 8 rotary switches (wired or CAN input) with each of 10 positions simultaneously mappable for pit switch, launch control, anti-lag, traction, traction target and traction control range, auxiliary timing, race time reset, engine speed limit, accelerator pedal translation, ignition timing, fuel mixture target, boost limit.
- Analog tachometer output with configurable output pin and scale.
- Drive by Wire dual bank throttle servo control.
- Accelerator pedal sensor with translation table.
- Use of an accelerator pedal sensor or a throttle position sensor in the case of a cable throttle.
- Transmission pump output with transmission temperature threshold and hysteresis control.
- Traction control with tables for Aim Main, Aim Compensation and Control Range.
- Measuring vehicle speed using wheel speed sensors, estimation or GPS.
- Vehicle speed limit control system (based on DBW accelerator), which can also be used for well speed limitation.
- Configurable warning system with light output and CAN.
- Auxiliary timing system with tables for ignition timing compensation, fuel volume compensation and fuel mixture target.
- Supports sequential and batch fuel injection.
- GPS acquisition and recording via CAN or RS232.
- 4 auxiliary outputs for PWM control of actuators added:
- Duty cycle tables using engine speed and throttle or manifold pressure shafts
- Activation based on intake manifold pressure or throttle position
- Auxiliary Output 1 includes tables for Ignition Timing Compensation, Fuel Volume Compensation, and Fuel Mixture Target
- Optional channels for additional sensors via input pin and/or CAN message, including:
- Airbox mass flow, pressure and temperature
- Ambient pressure and temperature
- Boost pressure
- Front and rear brake pressure
- Brake switch
- Clutch pressure and position
- Clutch switch
- Coolant pressure and temperature
- Engine oil pressure and temperature
- Engine crankcase pressure
- Exhaust Pressure Bank 1 and Bank 2
- Exhaust Temperature (EGT) via TCA thermocouple amplifier, generic CAN or E888 for manifold, bank 1 and 2 manifold and cylinders 1 through 8 (M150/M190: 12)
- Exhaust lambda via LTC, LTCN or PLM to manifold, bank 1 and 2 manifold and cylinders 1 to 8 (M150/M190: 12)
- Fuel pressure and temperature
- Fuel tank level
- Gear position
- Gear lever force
- Gear neutral switch
- Gear change request
- Intercooler temperature
- Steering angle and pressure
- Transmission pressure and temperature
- Turbocharger speed
- Turbocharger inlet/outlet temperature
- Turbocharger wastegate position
- G-force (acceleration) – Longitudinal, Lateral, Vertical
- Front/rear left/right wheel speed sensors, wired or CAN input.
Engine Rotation Modes
Starting with M1 System 1.4.00.0104
- AMC 242 – Jeep Cherokee XJ/XI (1994-2000), Jeep Wrangler TJ
- Aston Martin AJ37
- BMW M62TU V8
- BMW M54
- BMW N55 – BMW N55 and N52 engines
- BMW S1000RR MY2015
- BMW S50 – BMW S50B32 (E36M3)
- BMW S62 – BMW E36 M3 S52B32, BMW E46 M3 S64B32, BMW E39 M5 S62B50 NOTE: Untested – contact MoTeC before operating this engine
- BMW S85 – BMW E60 M3 S85B50, BMW E90 M3 S65B40
- Bosch 140 40 – General Motors LLT, Audi BXA / Lamborghini LP560, Mazda L3-VDT
- Bosch 140 40 36M1 – Polaris RZR Pro R (2022)
- Bosch 140 40 36M2 – Polaris Rebel (2021)
- Bosch 140 40 Alternative
- Bosch 60 120 180
- Camshaft one missing four stroke
- Camshaft two missing four strokes
- Chrysler Pentastar
- 2005 Chrysler SRT8 – 2005-2010 Chrysler 6.1l Hemi (e.g. Chrysler 300C SRT-8, Dodge Challenger SRT-8)
- Chrysler SRT8 2011 – Chrysler “Apache” 6.4l Hemi with variable valve timing 2011- (e.g. Chrysler 300C SRT-8, Dodge Challenger SRT-8)
- Corvette C4 ZR1 – GM LT5 (1990 – 1995)
- Crankshaft 12P15 Two Stroke
- Crankshaft One Missing Four Strokes
- Crankshaft One Missing Two Strokes
- Crankshaft Two Missing Four Strokes
- Crankshaft Two Missing Two Strokes
- Cummins B Series – Dodge Ram 2500, 3500, 4500 trucks equipped with ISB engines (2003-), Cummins QSB marine engines, Cummins QSB off-highway engines
- Custom EJ20G – Subaru GC8 WRX and STi (EJ20G, EJ20K, EJ207 etc.) from MY95 – MY00 with MY01 crankshaft sprocket (part number 13021AA141)
- Denso 270 90
- Denso 270 90 Magnetic
- Dodge the Viper
- Dodge Viper MY2008
- Fiat TwinAir
- Ford Cosworth YB
- Ford Coyote
- Ford Coyote GEN3 – Ford Mustang GT (2018-)
- Ford Cyclone – Ford F150 (2011-2016), Ford Expedition (2015-2016), Ford Racing M-6007-35T 3.5L V-6 Ecoboost crate engine
- Ford Duratec Synchronization – Duratec Cameras, EcoBoost, BA
- Ford Falcon I6 – (Ford Falcon EA-ED)
- Ford Nano – Ford Raptor (2017-), Ford GT (2017-)
- Ford Navistar T444E – Ford Powerstroke 7.3L Diesel (1994-2003)
- Ford Sigma TiVCT
- Ford Windsor – with 'PIP' sensor in the distributor
- Formula Renault V6
- Gastech TX1
- Gastech TX2
- General Motors DMAX LMM – General Motors 6.6L Duramax LMM diesel engines (late 2007 – early 2011) when the eighth digit of the VIN number is 6.
- General Motors LLR – H3 Hummer (2007 – 2010)
- General Motors LN3 – (Holden Commadore VN-VT)
- General Motors LS1 – (Gen 3 V8)
- General Motors LS7
- Gibson ZA348
- Honda Bike Synchronization
- Honda CBR250RR – Honda CBR250RR 2017
- Honda F20C (Honda S2000)
- Honda J32A (Acura TL & CL)
- Honda J35A
- Honda K20
- Honda K20C1 – Civic Type R 2015+
- Honda K24Z7
- Honda L15B7 – Honda Civic (2016-)
- Honda Marine BF250D
- Honda S07A – Honda S660 Roadster (2015-).
- Hyundai Gamma T GDI
- Hyundai Lambda II RS GDi engine (Hyundai Genesis V6)
- Hyundai Lambda II T GDI – KIA Stinger (2016-)
- Isuzu 4JK1
- Kia G4TH
- KTM SXF – KTM SX-F, Honda CRF250R, Suzuki RMZ250 (2016), Kawasaki KX250F (2013)
- Lamborghini V10 – Experimental mode for 5.0L port injected Gallardo 2003 – 2007
- Lamborghini LP520
- Mazda BP Z3 – MX5 NB (2001-2005)
- Mazda L3 – Mazda L3 VVTi (e.g. Mazda 3 SPorts SP23, Mazda 6), Ford Duratec 23EW iVCT (e.g. Ford Fusion CD338)
- Mazda MX5 2006: Mazda LF (MZR family) in MX5 NC (2006-), Suzuki M16A VVT in Swift Sport (2012-)
- Mazda RX8 – Mazda Renesis 13B-MSP
- Mazda SkyActiv G – Mazda6 GJ 2012+, MX5 ND 2015+, Mazda3 BM 2014+, Mazda2 DJ 2014+
- Mercedes M120 – 6.0l V12 (S600 1992 – 2001)
- Mercruiser 1075
- Mitsubishi 4B11 – Lancer Evolution X
- Mitsubishi 4G63T
- Mitsubishi 6A12 – 6A12, 6A13, 6G74, 6G75
- Mitsubishi Fuso 4P10 (also Agco Sisu Power 49G)
- Mitsubishi Fuso 6M60 – 2015 Fuso TKG-FK61F
- Multi Tooth Four Stroke
- Multi Tooth Two Stroke
- Nissan MR16DDT
- Nissan MR20DD (Nissan Sentra 2010-)
- Nissan RB26 – Nissan RB26 and other six-cylinder engines with 360-degree optical camshaft trigger
- Nissan SR20 – Nissan SR20, CA18DET and other four-cylinder engines with 360-degree optical camshaft trigger
- Nissan One wide slot – Nissan RB30 and other engines with 360 degree optical camshaft trigger
- Nissan VK50VE
- Nissan VK56DE – Nissan VK56DE engine and others
- Nissan VQ35 – Nissan VQ35HR engine, Nissan VR38DETT engine used in the 2007 R35 GTR
- Nissan VR30DDTT
- Nissan YS23DDT
- Peugeot PSA EW10 J4S – Peugeot 206 GTi and RC (2003-2007)
- Polaris RMK snowmobile – Two-stroke, two-cylinder (2014- ), including turbo versions
- Porsche 997: Porsche Direct Injected engine, 2009 Porsche GT2 with 3.6 Lt engine (Variocam PLUS)
- Private 1 – Private 6
- PSA EP6DTS – Mini Cooper S Turbo (2007-2010) and Peugeot 207 RC/GTI (2006-2010)
- Renault F4R – Clio Sport RS 3 (2005-2012)
- Rotax BRP 2 Stroke
- Rover K Series – Lotus Elise (1996-2001), Lotus Elise 111S (1999-2004)
- Scania DC16
- Scania SGL12A
- Subaru EA82 – Subaru Leone (1984-1994), Subaru XT (1985-1991)
- Subaru EJ207AVCS – Subaru EJ205, EJ207, EJ255, EJ257 from MY01 to MY05
- Subaru EJ20G – Subaru GC8 WRX and STi (EJ20G, EJ20K, EJ207 etc.) from MY95 – MY00
- Subaru EZ30 – EZ30D with Dual AVCS
- Subaru FA20D – Subaru EJ205, EJ207 etc. with dual AVCS (MY06-), Subaru FA20D for BRZ and FT86 (2012-)
- Subaru FA20DIT – Subaru Forester 2014, WRX 2015
- Suzuki K6A – Caterham 7 160, Suzuki Swift GT (2016 Indonesia)
- Toyota 1FZ FE – Toyota Landcruiser
- Toyota 1GD FTV
- Toyota 1KD FTV
- Toyota 1UZ-FE
- Toyota 2GR-FE – Lotus Evora, 3GR-FE etc, V6 with double VVT-i.
- Toyota 2JZ GE – Toyota 6 cylinder 2JZ-GE with VVT (example Lexus IS300)
- Toyota 2UR-GSE on Lexus RC-F 2015 MY (2014/09 -)
- Toyota 2ZR – Lotus Elise (2012-), Lexus RC 300 (2015-)
- Toyota 2ZZ – Toyota 2ZZ, 3GS and others with VVT.
- Volkswagen EA189
- Volkswagen EA211 – Volkswagen Golf mk7 (2015-)
- Volvo B4204T9
- Volvo B5244S
- Volvo D11C – D11C truck engine (FM450 Platform)
- Yamaha FX SHO
- Bosch 140 40 Alternative – 36M1, 36M2
- BMW M62TUB44
- Cosworth AG2
- Honda UTV 999cc – (Honda Talon (2016-2021), Honda Pioneer (2016-2021)
- Synergy V8 – based on S1000RR (2020-)
- Rover/MG K-series 1.4L without timing sensor.
Pinout Example
M150 A connector – 34 ways
Mating connector: Tyco Superseal 34 Position Keying 2 – MoTeC # 65067
Pin | Designation | Full name | Function |
---|---|---|---|
A01 | AT5 | Analog Temperature Input 5 | 1k Pull up to SEN_5V_C |
A02 | AT6 | Analog temperature input 6 | 1k Pull up to SEN_5V_C |
Answer A03 | AV15 | Analog voltage input 15 | |
A04 | AV16 | Analog voltage input 16 | |
A05 | AV17 | Analog voltage input 17 | |
A06 | IGN_LS9 | Low side ignition 9 | |
A07 | IGN_LS10 | Low side ignition 10 | |
A08 | IGN_LS11 | Low side ignition 11 | |
A09 | IGN_LS12 | Low side ignition 12 | |
Answer 10 | SEN_5V0_C1 | 5.0VC Sensor | |
Answer 11 | LA_NB1 | Lambda narrow input 1 | |
Answer 12 | LA_NB2 | Lambda 2 Narrow Entry | |
Answer 13 | BEAT 3 | Detonation input 3 | |
Answer 14 | BEAT 4 | Detonation input 4 | |
Answer 15 | DIG2 | Digital input 2 | |
Answer 16 | DIG3 | Digital input 3 | |
Answer 17 | DIG4 | Digital input 4 | |
Answer 18 | SEN_5V0_C2 | 5.0VC Sensor | |
A19 | SEN_5V0_B2 | 5.0VB Sensor | |
Answer 20 | LIN | LIN Bus | |
A21 | RS232_RX | RS232 Receive | |
ANSWER 22 | RS232_TX | RS232 transmission | |
A23 | DIG1 | Digital input 1 | |
A24 | BAT_NEG3 | Negative Battery | |
A25 | BAT_NEG4 | Negative Battery | |
A26 | SEN_0V_C1 | Sensor 0V C | |
A27 | SEN_0V_C2 | Sensor 0V C | |
A28 | CAN3_HI | CAN Bus 3 High | |
A29 | CAN3_LO | CAN Bus 3 Low | |
Answer 30 | CAN2_HI | CAN Bus 2 High | |
A31 | CAN2_LO | CAN Bus 2 Low | |
A32 | BAT_NEG5 | Negative Battery | |
A33 | SEN_0V_B1 | Sensor 0V B | |
Answer 34 | SEN_0V_A1 | Sensor 0V A |
M150 Connector B – 26-way
Mating connector: Tyco Superseal 26 Position Keying 3 – MoTeC # 65068
Pin | Designation | Full name | Usage example |
---|---|---|---|
B01 | OUT_HB9 | Half bridge exit 9 | |
B02 | OUT_HB10 | Half bridge exit 10 | |
B03 | UDIG8 | Universal digital input 8 | |
B04 | UDIG9 | Universal Digital Input 9 | Engine running switch |
B05 | UDIG10 | Universal Digital Input 10 | |
B06 | UDIG11 | Universal Digital Input 11 | |
B07 | UDIG12 | Universal digital input 12 | |
B08 | INJ_LS5 | Low Side Injector 5 | |
B09 | INJ_LS3 | Low Side Injector 3 | |
B10 | AV9 | Analog voltage input 9 | |
B11 | AV10 | Analog voltage input 10 | |
B12 | AV11 | Analog voltage input 11 | |
B13 | BAT_POS | Positive Battery | ECU battery voltage |
B14 | INJ_LS6 | Low Side Injector 6 | |
B15 | INJ_LS4 | Low Side Injector 4 | |
B16 | AV12 | Analog voltage input 12 | |
B17 | AV13 | Analog voltage input 13 | |
B18 | AV14 | Analog voltage input 14 | |
B19 | BAT_POS | Positive Battery | ECU battery voltage |
B20 | OUT_HB7 | Half bridge exit 7 | Fuel pump outlet |
B21 | OUT_HB8 | Half bridge exit 8 | |
B22 | INJ_PH9 | Peak retention injector 9 | |
B23 | INJ_PH10 | Peak retention injector 10 | |
B24 | INJ_PH11 | Peak retention injector 11 | |
B25 | INJ_PH12 | Peak retention injector 12 | |
B26 | SEN_5V0_A | 5.0VA Sensor |
M150 C connector – 34 ways
Mating connector: Tyco Superseal 34 Position Keying 1 – MoTeC #65044
Pin | Designation | Full name | Usage example |
---|---|---|---|
C01 | OUT_HB2 | Half bridge exit 2 | Throttle servo bank 1 motor output |
C02 | SEN_5V0_A | 5.0VA Sensor | |
C03 | IGN_LS1 | Low side ignition 1 | Ignition cylinder 1 output |
C04 | IGN_LS2 | Low Side Ignition 2 | Ignition cylinder 2 output |
C05 | IGN_LS3 | Low side ignition 3 | Ignition Cylinder 3 Output |
C06 | IGN_LS4 | Low side ignition 4 | Ignition Cylinder 4 Output |
C07 | IGN_LS5 | Low side ignition 5 | Ignition cylinder 5 outputs |
C08 | IGN_LS6 | Low side ignition 6 | Ignition cylinder 6 outputs |
C09 | SEN_5V0_B | 5.0VB Sensor | |
C10 | BAT_NEG1 | Negative Battery | |
C11 | BAT_NEG2 | Negative Battery | |
C12 | IGN_LS7 | Low Side Ignition 7 | Ignition Cylinder 7 Output |
C13 | IGN_LS8 | Low side ignition 8 | Ignition cylinder 8 outputs |
C14 | AV1 | Analog voltage input 1 | Main 1 Position Servo Throttle Bank |
C15 | AV2 | Analog voltage input 2 | Intake manifold pressure sensor |
C16 | AV3 | Analog voltage input 3 | Throttle servo bank 1 position tracking |
C17 | AV4 | Analog voltage input 4 | |
C18 | OUT_HB1 | Half bridge exit 1 | Throttle servo bank 1 motor output |
C19 | INJ_PH1 | Peak retention injector 1 | Fuel cylinder outlet 1 |
C20 | INJ_PH2 | Peak retention injector 2 | Fuel cylinder outlet 2 |
C21 | INJ_PH3 | Peak retention injector 3 | Fuel cylinder outlet 3 |
C22 | INJ_PH4 | Peak retention injector 4 | Fuel Cylinder 4 Outlet |
C23 | INJ_LS1 | Low Side Injector 1 | |
C24 | INJ_LS2 | Low Side Injector 2 | |
C25 | AV5 | Analog voltage input 5 | |
C26 | BAT_POS | Positive Battery | ECU battery voltage |
C27 | INJ_PH5 | Peak retention injector 5 | Fuel Cylinder 5 Outlet |
C28 | INJ_PH6 | Peak retention injector 6 | Fuel cylinder outlet 6 |
C29 | INJ_PH7 | Peak retention injector 7 | Fuel Cylinder 7 Outlet |
C30 | INJ_PH8 | Peak retention injector 8 | Fuel cylinder outlet 8 |
C31 | OUT_HB3 | Half bridge exit 3 | Inlet 1 Outlet Camshaft Actuator Bank |
C32 | OUT_HB4 | Half bridge exit 4 | Inlet 2 Outlet Camshaft Actuator Bank |
C33 | OUT_HB5 | Half bridge exit 5 | Exhaust Camshaft Bank 1 Actuator Output |
C34 | OUT_HB6 | Half bridge exit 6 | Exhaust Camshaft Bank 2 Actuator Output |
M150 Connector D — 26 Ways
Mating connector: Tyco Superseal 26 Position Keying 1 – MoTeC # 65045
Pin | Designation | Full name | OE pin | Function | Usage example |
---|---|---|---|---|---|
D01 | UDIG1 | Universal digital input 1 | Engine speed sensor | ||
D02 | UDIG2 | Universal digital input 2 | |||
D03 | AT1 | Analog temperature input 1 | 1k Pull up to SEN_5V_A | Intake manifold temperature sensor | |
D04 | AT2 | Analog temperature input 2 | 1k Pull up to SEN_5V_A | Coolant temperature sensor | |
D05 | AT3 | Analog Temperature Input 3 | 1k Pull up to SEN_5V_B | Engine oil temperature sensor | |
D06 | AT4 | Analog temperature input 4 | 1k Pull up to SEN_5V_B | ||
D07 | BEAT 1 | Detonation input 1 | Knock sensor 1 | ||
D08 | UDIG3 | Universal Digital Input 3 | Intake Camshaft Bank 1 Position | ||
D09 | UDIG4 | Universal digital input 4 | Exhaust camshaft bank 1 position | ||
D10 | UDIG5 | Universal Digital Input 5 | Intake Camshaft Bank 2 Positions | ||
D11 | UDIG6 | Universal Digital Input 6 | Exhaust Camshaft Bank 2 Positions | ||
D12 | BAT_BAK | Battery Backup | |||
D13 | BEAT 2 | Detonation input 2 | Knock sensor 1 | ||
D14 | UDIG7 | Universal digital input 7 | |||
D15 | SEN_0V_A | Sensor 0V A | |||
D16 | SEN_0V_B | Sensor 0V B | |||
D17 | CAN1_HI | CAN Bus 1 High | |||
D18 | CAN1_LO | CAN Bus 1 Low | |||
D19 | SEN_6V3 | 6.3V Sensor | |||
D20 | AV6 | Analog voltage input 6 | |||
D21 | AV7 | Analog voltage input 7 | Main accelerator pedal sensor | ||
D22 | AV8 | Analog voltage input 8 | Accelerator pedal sensor tracking | ||
D23 | ETH_TX+ | Ethernet+ transmission | Green/White Ethernet | ||
D24 | ETH_TX- | Ethernet Transmission- | Green Ethernet | ||
D25 | ETH_RX+ | Ethernet+ reception | Orange/White Ethernet | ||
D26 | ETH_RX- | Ethernet Reception- | Ethernet |
M130 A connector — 34 ways
Mating connector: Tyco Superseal 34 Position Keying 1 – MoTeC #65044Pin | Designation | Full name | Usage example |
---|---|---|---|
A01 | OUT_HB2 | Half bridge exit 2 | |
A02 | SEN_5V0_A | 5.0VA Sensor | |
Answer A03 | IGN_LS1 | Low side ignition 1 | Ignition cylinder 1 and 4 outlets |
A04 | IGN_LS2 | Low Side Ignition 2 | Ignition cylinder 2 and 3 outlets |
A05 | IGN_LS3 | Low side ignition 3 | |
A06 | IGN_LS4 | Low side ignition 4 | |
A07 | IGN_LS5 | Low side ignition 5 | |
A08 | IGN_LS6 | Low side ignition 6 | |
A09 | SEN_5V0_B | 5.0VB Sensor | |
Answer 10 | BAT_NEG1 | Negative Battery | |
Answer 11 | BAT_NEG2 | Negative Battery | |
Answer 12 | IGN_LS7 | Low Side Ignition 7 | |
Answer 13 | IGN_LS8 | Low side ignition 8 | |
Answer 14 | AV1 | Analog voltage input 1 | Main 1 Position Servo Throttle Bank |
Answer 15 | AV2 | Analog voltage input 2 | Intake manifold pressure sensor |
Answer 16 | AV3 | Analog voltage input 3 | |
Answer 17 | AV4 | Analog voltage input 4 | Air box mass flow sensor |
Answer 18 | OUT_HB1 | Half bridge exit 1 | |
A19 | INJ_PH1 | Peak retention injector 1 | Fuel cylinder outlet 1 |
Answer 20 | INJ_PH2 | Peak retention injector 2 | Fuel cylinder outlet 2 |
A21 | INJ_PH3 | Peak retention injector 3 | Fuel cylinder outlet 3 |
ANSWER 22 | INJ_PH4 | Peak retention injector 4 | Fuel Cylinder 4 Outlet |
A23 | INJ_LS1 | Low Side Injector 1 | Fuel pump outlet |
A24 | INJ_LS2 | Low Side Injector 2 | |
A25 | AV5 | Analog voltage input 5 | |
A26 | BAT_POS | Positive Battery | ECU battery voltage |
A27 | INJ_PH5 | Peak retention injector 5 | |
A28 | INJ_PH6 | Peak retention injector 6 | |
A29 | INJ_PH7 | Peak retention injector 7 | |
Answer 30 | INJ_PH8 | Peak retention injector 8 | |
A31 | OUT_HB3 | Half bridge exit 3 | |
A32 | OUT_HB4 | Half bridge exit 4 | |
A33 | OUT_HB5 | Half bridge exit 5 | Tachometer output |
Answer 34 | OUT_HB6 | Half bridge exit 6 | Normal idle actuator solenoid output |
M130 Connector B — 26-way
Mating connector: Tyco Superseal 26 Position Keying 1 – MoTeC # 65045Pin | Designation | Full name | OE pin | Function | Usage example |
---|---|---|---|---|---|
B01 | UDIG1 | Universal digital input 1 | Engine speed | ||
B02 | UDIG2 | Universal digital input 2 | Engine synchronization | ||
B03 | AT1 | Analog temperature input 1 | 1k Pull up to SEN_5V_A | ||
B04 | AT2 | Analog temperature input 2 | 1k Pull up to SEN_5V_B | Coolant temperature sensor | |
B05 | AT3 | Analog Temperature Input 3 | 1k Pull up to SEN_5V_A | Fuel temperature sensor | |
B06 | AT4 | Analog temperature input 4 | 1k Pull up to SEN_5V_B | Intake manifold temperature sensor | |
B07 | BEAT 1 | Detonation input 1 | Knock sensor 1 | ||
B08 | UDIG3 | Universal Digital Input 3 | Rear wheel speed sensor | ||
B09 | UDIG4 | Universal digital input 4 | |||
B10 | UDIG5 | Universal Digital Input 5 | |||
B11 | UDIG6 | Universal Digital Input 6 | |||
B12 | BAT_BAK | Battery Backup | |||
B13 | BEAT 2 | Detonation input 2 | |||
B14 | UDIG7 | Universal digital input 7 | |||
B15 | SEN_0V_A | Sensor 0V A | |||
B16 | SEN_0V_B | Sensor 0V B | |||
B17 | CAN_HI | CAN Bus 1 High | |||
B18 | CAN_LO | CAN Bus 1 Low | |||
B19 | SEN_6V3 | 6.3V Sensor | |||
B20 | AV6 | Analog voltage input 6 | |||
B21 | AV7 | Analog voltage input 7 | |||
B22 | AV8 | Analog voltage input 8 | |||
B23 | ETH_TX+ | Ethernet+ transmission | Green/White Ethernet | ||
B24 | ETH_TX- | Ethernet Transmission- | Green Ethernet | ||
B25 | ETH_RX+ | Ethernet+ reception | Orange/White Ethernet | ||
B26 | ETH_RX- | Ethernet Reception- | Orange Ethernet |